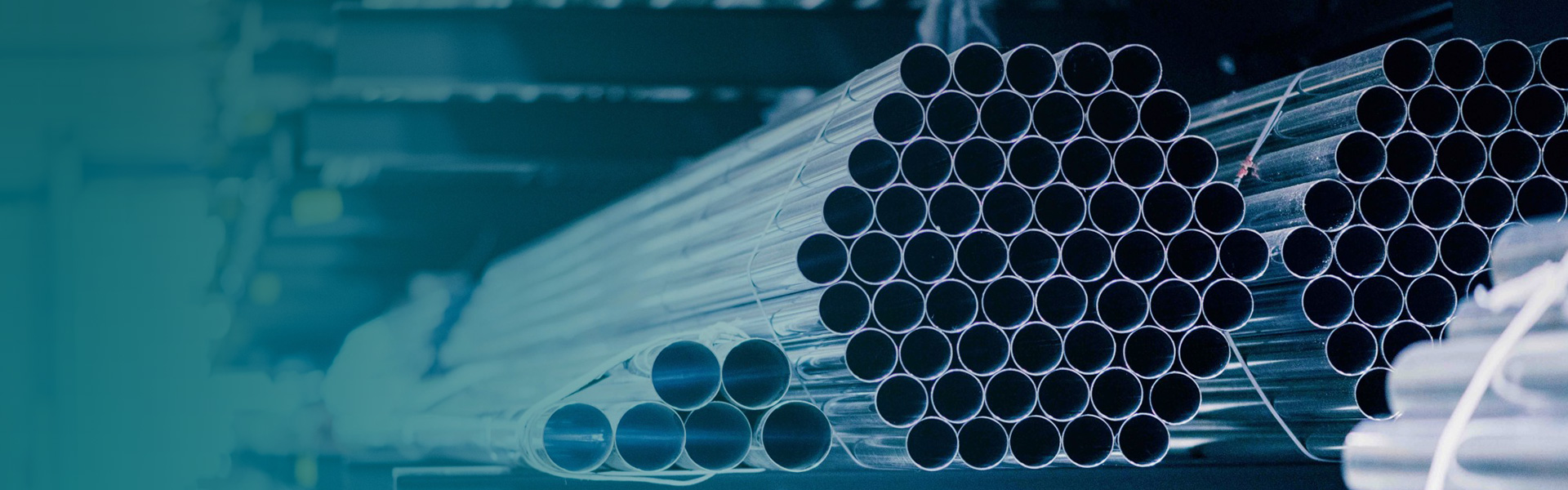
Alloy
A high-tech enterprise focusing on the development and application of X-ray technology products, committed to becoming a leading supplier of X-ray industrial testing solutions.
The Future of Metal Analyzers: Trends and Innovations in Technology
The world of industrial analysis is evolving rapidly, and metal analyzers are at the forefront of this technological revolution. From ensuring product quality in manufacturing to maintaining the integrity of infrastructure, metal analysis plays a crucial role in a wide array of industries, including aerospace, automotive, pharmaceuticals, and even environmental monitoring. As demand for more accurate and efficient analysis grows, innovations in metal analyzer technology are poised to redefine how we measure, assess, and interact with metallic materials.
1. Integration of Artificial Intelligence (AI) and Machine Learning
One of the most transformative advancements in the future of metal analyzers is the integration of artificial intelligence (AI) and machine learning (ML). By incorporating AI into metal analyzers, the systems can analyze data faster, more accurately, and even predict potential failures or quality issues before they arise.
AI-powered metal analyzers are able to recognize patterns in data that traditional systems may miss, leading to enhanced detection of defects, inconsistencies, and impurities within metals. These smart systems can learn from previous tests, improve over time, and offer more reliable results. This automation can drastically reduce human error, making the analysis process not only quicker but also more efficient and consistent.
2. Portable and Real-time Analysis
Traditionally, metal analysis involved sending samples to a lab for testing, which could take days or even weeks. This process has been slow and limited in terms of real-time decision-making. However, portable metal analyzers are changing the game by enabling real-time, on-site analysis.
These portable devices, often handheld or mobile, allow for immediate assessment of metal composition and quality in the field. Whether on a factory floor or at a construction site, metal analysts can now perform tests directly where the material is located, allowing for faster decision-making and minimizing downtime.
Furthermore, advancements in sensor technology and miniaturization are making these devices more accurate while reducing their size and cost. Real-time data from portable analyzers can now be transmitted to cloud-based platforms for further analysis, allowing teams to make collaborative decisions instantly, no matter where they are.
3. Improved Sensitivity and Accuracy with Advanced Spectroscopy
Spectroscopic techniques have long been central to metal analysis, allowing for the determination of elemental composition and structure. As technology advances, spectroscopy is becoming even more precise.
Next-generation X-ray fluorescence (XRF) spectrometers, for example, are evolving to offer increased sensitivity, enabling the detection of trace elements that were previously undetectable. These spectrometers are now capable of analyzing complex alloys with unprecedented accuracy, making them essential in industries like aerospace, where high-strength materials must meet strict specifications.
In addition, optical emission spectrometry (OES) is also benefiting from improvements in resolution and sensitivity, making it a valuable tool for real-time and high-throughput testing of metals used in critical applications.
4. AI-Driven Predictive Maintenance and Condition Monitoring
Another promising innovation on the horizon is the integration of predictive maintenance into metal analyzer systems. By utilizing real-time data and analytics, metal analyzers can provide predictive insights into the health and longevity of metallic materials, structures, or machinery.
For example, sensors embedded in metal objects or equipment can continuously monitor stress, wear, corrosion, and fatigue over time. These sensors feed data back to AI systems that analyze the information to predict when a failure is likely to occur, allowing for timely intervention before a catastrophic breakdown happens.
This predictive approach not only enhances safety but also reduces maintenance costs and increases operational efficiency. For industries where downtime can be extremely costly, the ability to forecast potential failures and take preventive measures could save millions of dollars in repairs and lost productivity.
5. Enhanced Data Analytics and Cloud Integration
As metal analyzers become more connected, they will increasingly rely on cloud computing for data storage and analysis. Cloud-based platforms can aggregate vast amounts of data from multiple analyzers, creating centralized databases for better data management and analysis.
With cloud integration, metal analyzers can not only store large amounts of test data but also process and analyze it using advanced analytics tools. Users will be able to access real-time information remotely, track long-term trends, and collaborate seamlessly across global teams. This level of connectivity will enable faster decision-making and greater collaboration between different departments, ensuring that any issues with metal materials can be addressed quickly and accurately.
Additionally, AI-driven cloud platforms will offer advanced predictive modeling and trend analysis, helping industries make data-driven decisions about metal usage, procurement, and production processes.
6. Environmental Sustainability in Metal Analysis
As the world shifts toward more sustainable practices, the role of metal analyzers in environmental monitoring will become even more significant. Metal analysis plays a key role in monitoring pollution levels, particularly in water and soil testing. With growing concerns about the environmental impact of industrial activities, there is an increasing need for accurate, real-time analysis of metal contaminants in the environment.
Innovative analyzers are being developed with eco-friendly features, such as reduced energy consumption and the use of non-toxic chemicals. Portable, energy-efficient models that are capable of performing quick environmental analysis will be in high demand, particularly in remote areas where access to traditional labs is limited.
The advancement of recycling technology will also be bolstered by better metal analysis. With the increasing need for sustainable manufacturing, the ability to recycle and repurpose metals will rely heavily on efficient and accurate analysis to ensure that materials are reused properly.
Terras EulerX900 Handheld Alloy Analyzer
For decades, XRF spectrometry has been essential for metal analysis, prized for its speed, accuracy, and ease of use in quality control. The EulerX 900 series excels with cutting-edge technology, providing lab-quality results in seconds without sample prep. Its user-friendly interface displays alloy grades and compositions on the spot, streamlining inspections of raw materials, finished goods, and production parts. Versatile enough for solids, liquids, and powders, it’s widely used in scrap sorting, precious metals testing, PMI, and more.
Conclusion
The future of metal analyzers is incredibly promising, driven by advancements in AI, real-time data analysis, and more accurate measurement techniques. With smarter, faster, and more portable devices on the horizon, industries across the globe are set to benefit from enhanced material analysis capabilities.
Join Us
Subscribe to our email list for updates & promotions.