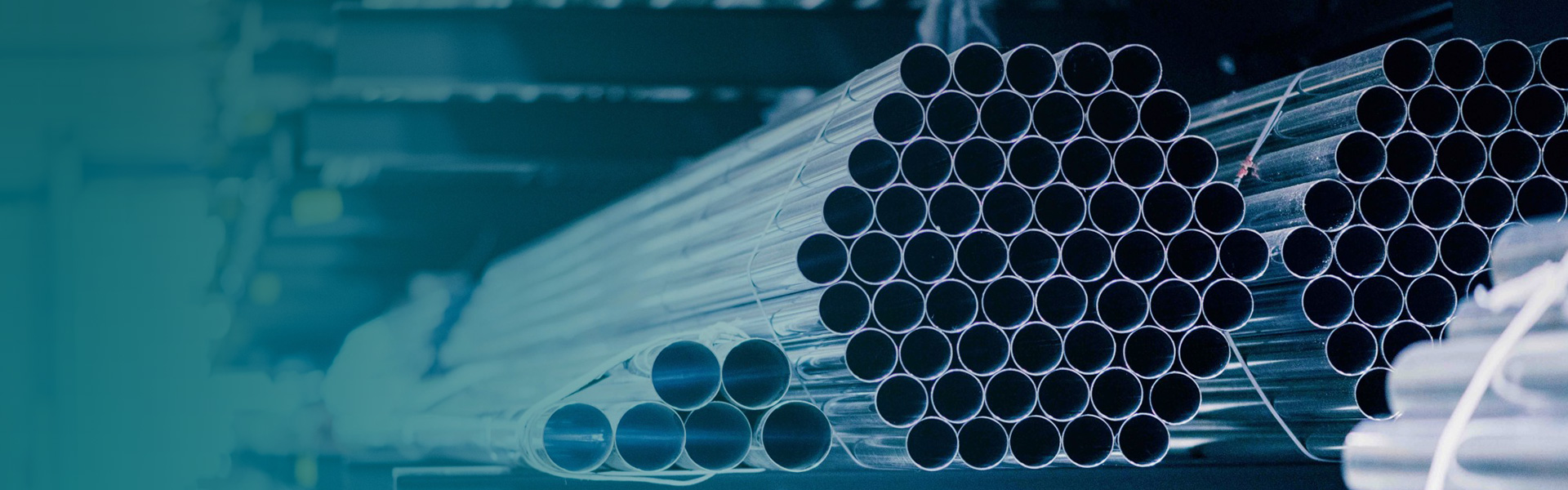
Alloy
A high-tech enterprise focusing on the development and application of X-ray technology products, committed to becoming a leading supplier of X-ray industrial testing solutions.
How a Metal Purity Tester Can Ensure Accurate Metal Quality Control——XRF technology
In industries where metal purity is critical, such as aerospace, automotive, and electronics, ensuring the highest standards of quality control is vital. One of the most effective tools for achieving this is the Metal Purity Tester using X-ray Fluorescence (XRF) technology. XRF has become a game-changer in the realm of metal analysis due to its precision, speed, and non-destructive nature. This article delves into how a metal purity tester using XRF technology can ensure accurate metal quality control.
What is XRF Technology?
X-ray Fluorescence (XRF) is a non-destructive analytical technique that identifies the elemental composition of materials. When a metal sample is exposed to X-rays, it emits secondary (or fluorescent) X-rays. These fluorescent X-rays are unique to each element in the metal, enabling precise identification and quantification of the elements present. XRF technology has a wide range of applications in metal testing, from detecting trace elements to determining the overall composition of alloys.
The Role of Metal Purity Testers in Quality Control
In manufacturing, the purity of metal directly affects product performance, durability, and safety. Therefore, quality control during the production process is essential to avoid defects and ensure that metals meet the necessary specifications. Metal purity testers are specialized devices designed to assess metal quality by analyzing its elemental composition.
With XRF technology, metal purity testers provide a quick and reliable method of analyzing metals on-site or in the lab. By evaluating the purity of metals, these testers help to verify that the materials meet industry standards, regulatory requirements, and the expectations of customers.
Key Benefits of Using XRF Technology in Metal Purity Testing
1. High Accuracy and Precision
XRF technology offers an extremely high level of accuracy, making it ideal for assessing the quality of metals used in precision industries. It can detect even trace amounts of impurities in metals, ensuring that the material meets strict purity requirements. This precision is critical in industries like aerospace, where even the smallest impurity can compromise the safety and performance of critical components.
2. Non-Destructive Testing
Unlike traditional methods that may require sample destruction or extensive preparation, XRF is non-destructive. This means that the metal sample remains intact and can be used in the manufacturing process after testing. This feature is particularly beneficial in industries where expensive materials are being tested, as it prevents waste and ensures the continued integrity of the sample.
3. Rapid Results
One of the most significant advantages of XRF technology is the speed at which results can be obtained. With XRF metal purity testers, you can receive real-time data about the composition of a metal sample, often within minutes. This quick turnaround time is essential for maintaining efficient production processes and avoiding delays in manufacturing.
4. Ease of Use
Modern XRF devices are designed to be user-friendly and require minimal training. Most metal purity testers are portable and come with intuitive interfaces, making it easy for operators to perform tests on-site without requiring specialized knowledge. The simplicity of the technology allows for seamless integration into existing quality control workflows.
5. Versatility
XRF technology is highly versatile and can be used to test a wide variety of metal alloys, including ferrous, non-ferrous, and precious metals. Whether you are testing steel, aluminum, copper, gold, or any other metal, XRF technology provides reliable results across many different materials.
Applications of XRF Metal Purity Testing
1. Material Certification
In industries where compliance with standards and certifications is mandatory, such as in aerospace or automotive manufacturing, XRF testing ensures that materials are up to spec. Metal purity testers confirm whether the metal alloys meet the required certifications for use in specific applications, such as ASTM or ISO standards.
2. Detecting Contaminants
XRF technology can detect contaminants that could compromise the quality of the metal, such as lead, mercury, or other toxic elements. This is particularly important for ensuring environmental safety and preventing harmful substances from entering production processes, such as in the electronics industry.
3. Recycling and Scrap Sorting
XRF technology plays a significant role in the recycling industry, where sorting and analyzing scrap metal is critical. Metal purity testers can quickly identify the composition of scrap metal, ensuring that valuable materials are accurately separated for reuse or sale. This process enhances recycling efficiency and helps prevent cross-contamination of metals.
Terras Pi900E Handheld Alloy Analyzer
4. Alloy Verification
In the manufacturing of metal products, verifying the composition of alloys is essential for ensuring that the final product meets the required specifications. XRF testing allows manufacturers to verify the alloy mix, ensuring that the correct proportions of metals are present for optimal performance and durability.
Designed for professionals, the Pi 900E Portable Alloy Analyzer delivers precise, rapid elemental analysis using XRF technology, perfect for scrap sorting, quality control, or lab testing. It provides instant results, Wi-Fi data transfer, and detailed alloy composition reports, covering elements from Mg to U. With a compact, durable build and user-friendly touchscreen, it’s optimized for portability and performance in tough field conditions.
Conclusion
As industries increasingly demand higher levels of metal purity and quality control, the role of metal purity testers utilizing XRF technology has become more crucial than ever. XRF offers a fast, accurate, and non-destructive solution for assessing the purity of metal materials, ensuring that they meet the stringent standards required in various industries. By incorporating XRF technology into quality control processes, manufacturers can enhance product reliability, reduce costly errors, and maintain compliance with industry regulations.
Join Us
Subscribe to our email list for updates & promotions.